Mechanical properties of 422 stainless steel repaired via wire feed laser welding
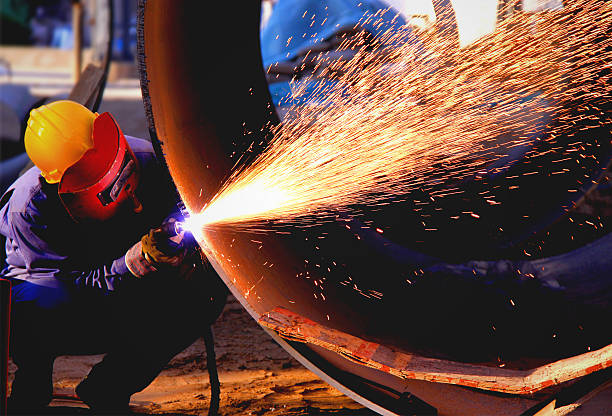
INTRODUCTION
Type 422 a modifed AISI 420 martensitic stainless steel, has a C content of 0.20 –0.25 wt-% with additions of carbide forming elements (Mo, V, and W) for high tem- perature strength. It is designed for service temperatures up to 650°C with a satisfactory combination of strength and toughness.
The steel is primarily used for turbine blades, high strength fasteners, and valves, as well as structural components in aircraft applications.Because of its chro- mium content (12 wt-%), it does not require protection against corrosion in service.
Type 422 stainless steel can be heat treated (quench and temper) to obtain a wide range of mechanical properties to meet the requirements ofa specific application, but welding of this material is not straightfor- ward owing to its crack sensitivity.
Therefore, appropriate precautions must be taken in welding procedures, such as control of preheating temperature, elimination of hydrogen pickup, and appropriate post-weld heat treatment (PWHT) to guarantee sound welds. Repair welding of damaged parts is one of the important applications of laser materials processing. Laser welding is characterisedby a short interaction time with intense energy density. As a result, the process has a low heat input and causes less distortion of the weldment than conventional welding processes. Laser repair of high cost components such as steam turbine blades is becoming attractive as an alternative to replacement. Ernst et al.reported the possibility of repairing cracks in dies via laser welding and Sun et al.demonstrated crack repair of a hot worked tool steel via laser melt processing. The use of fitller wire was proposed originally to overcome poor fitup problems in laser welding.A recent study6indicated that the stringent fitup requirements for laser welding can be relaxed some- what using filler wire additions. However, the addition of filler metal is necessary for repair applicationsto rebuild the damaged component to its original dimensions. In weld repairs, mechanical properties of the built up deposit are important because the filler metal is required to replace some of the original part that has been removed by machining. Ductile filler metals are often utilised for repair welding to minimise the strain imposed on the hardened heat affected zone (HAZ) and to compensatefor weld metal (WM) shrinkage. The purpose of the present investigation was to study the mechanical properties of 422 SS specimens laser repaired using 410 SS filler wire. Tensile, impact, and fatigue crack growth tests ofweld repairs were included in the evaluation process.Inaddition,microstructural andmechanical characterisations were conducted on a used 422 SS blade to determine the appropriate heat treatment procedure before carrying out a laser repair. The results obtained from the present work could be helpful for laser repair of damaged steam turbine blades, particularly for regions under low stress, especially in conjunctionwith furtherwork in progress.
MATERIAL AND EXPERIMENTAL PROCEDURE
MATERIAL AND EXPERIMENTAL PROCEDURES The alloy used in the present investigation was Carpenter 636 (type 422 SS) in the form of a 16 cm diameter bar. The chemical composition of the steel (wt-%) was 0.24C, 11.98Cr, 1.07Mo, 0.99W, 0.76Ni, 0.71Mn, 0.26V, 0.38Si, 0.016P, 0.006S, and balance Fe. Discs (4 mm in thickness), which were sliced from the bar, were austenitised at 1038°C in a vacuum furnace for 40 min and cooled to room temperature by purging the specimen chamber using high pressure nitrogen. Tempering of specimens was performed at 750°C for 2 h in a salt bath, followed by air cooling. Before laser repairing the Carpenter 636 specimens, microstructural andmechanical characterisations were performed on an intermediate pressure steam turbine blade (type 422 SS) after 20 years service at about 540°C in a fossil fuel power plant. Tensile and impact tests along with microstructural examinations of the used blade were carried out in the as received (20 years service at about 540°C) and heat treated (1038°C/40 min austenitised and 750°C/2 h tempered) conditions. Appropriate heat treat- ment before repairing was necessary to restore the original properties of the blade after long term service.
chematic conguration of repair welding syste
To simulate the laser repair process, a machinedV groove is introduced into the specimen as shown in Fig. 1. After Fitlling the groove with Fitller metal using the laser, a symmetrical groove, having a depth slightly greater than 2 mm, was made on the other side ofthe specimen and then welded again. In fact, the cross-section of such weld repairs was essentially the same as that of double V groove welds. No porosity in repaired specimens was found via metallo- graphic examinations. The repair welding in the present work was carried out using 410 SS Fitller wire (1.15 mm diameter). The nominal chemical composition of the wire (wt-%) was 0.095C, 12.98Cr, 0.52Ni, 0.47Mo, 0.43Mn, 0.39Si, 0.015P, 0.007S, and balance Fe. Weld repairs using 410 SS Fitller metal were designated as WR –410 specimens. A RoFitn –Sinar RS –850 5 kW CO2laser and Cyclomatic DWF –3 wire feeding system were used for repair welding. The schematic conFitguration for the complete system is shown in Fig. 2, in which the Fitller wire is introduced at the leading edge ofthe defocused laser beam at an angle of18°. For simplicity, only one welding pass was allowed to Fitll the groove. The preheat temperature was maintained at 250°C, and the specimen was held at this temperature for 1 h after completion of welding. The detailed welding parameters used in the experiment are given in Table 1. After repair welding, all specimens were subjected to a 700°C/2 h post- weld or stress relief heat treatment. Figure 3 is a schematic diagram showing the orientation oftensile, impact, and compacttension (CT) specimens with respect to the welding direction of the disc. The specimens for tensile and Charpy impact testing were produced
ientation of tensile, impact, and compact tension speci-mens with respect to welding direction of disc specimen
applications. The composition and the heat treatment procedure of the experimental material should be as close as possible tothose for aspecific component being considered for laser repair. Figure 4 shows the hardness versus tempering tempera- ture curves for the experimental material (Carpenter 636) and a used 422 blade after 1038°C/40 min solution heat treatment. These two similar curves revealed a secondary hardening between 400 and 500°C, and the alloys softened at tempering temperatures higher than 550°C. The hardness of the used blade inthe as received condition was 26.9 HRC, resembling the hardness of Carpenter 636 SS (25.5 HRC) and the used blade (26.1 HRC) that had been subjected to solution (1038°C/40 min) and temper (750°C/ 2 h) treatments. The results oftensile and impact testing ofthe used blade and Carpenter 636 SS are given in Table 2. It can be seen that the mechanical properties of the two alloys in the heat treated condition (1038°C/40 minz750°C/2 h) were simi- lar. Although the used blade in the as received condition had higher strength and lower ductility than that in the heat treated condition, the differences were relatively small. In contrast, the impact energy of the used blade (5.0 J) is considerably less than that of either the Carpenter 636 specimen (12.8 J) or the same blade after heat treatment (15.1 J) as can be seen in Table 2. From the results of hardness and mechanical tests, it could be concluded that the original heat treatment procedure for this particular blade was tempering at 750°C/2 h after a suitable solution