Study on Welding of Steel 17-4PH for Steam Turbine Blades
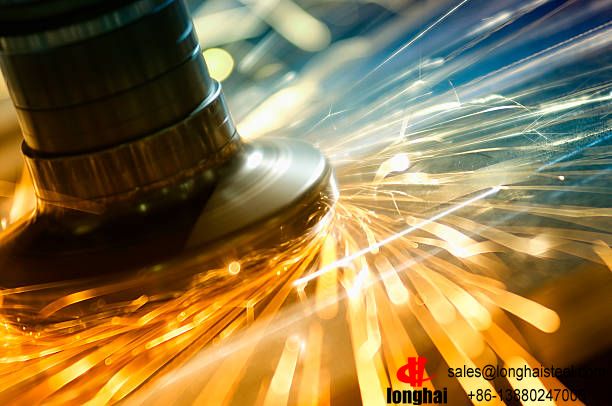
Harbin Steam Turbine Works Co., Ltd. self-optimized design of 300MW, 600MW steam turbine unit low-pressure final stage moving blade nominal length (profile part) is 1000mm, the material used for the blade is 17-4PH martensitic precipitation Hardened stainless steel, formed by semi-precision forging, the total length of the blank has reached 1132mm.
Harbin Steam Turbine Works Co., Ltd. has carried out a lot of domestic research work on this blade material twice, and has successively developed 510mm, 710mm, 865mm, 900mm and 1000mm (profile part) long blades, as 300MW, 600MW and 200MW retrofit the last or next-to-last stage blades of the unit, and these blades have been successfully and safely operated for many years. At present, the last-stage and second-last-stage blades of 300/600MW steam turbines are made of this material.
The grade of 17-4PH, which is a kind of martensitic precipitation hardening stainless steel. It was developed by Armco Company in the United States as early as the 1940s. Formed by this process, it has very low carbon content and high Cr and Ni content, which ensures that this steel can obtain a low-carbon martensite matrix with good plasticity; Celite matrix provides a dispersion strengthening phase - Cu-rich phase. Because of these two aspects, this steel has good comprehensive mechanical properties, excellent corrosion resistance and vibration attenuation performance, especially the latter is an important factor for the application of this steel in the low-pressure final stage moving blade of steam turbine.
According to the localization research and test work of this blade material, the normal temperature mechanical properties, metallographic structure, low-magnification structure and heat treatment process of this material have been fully grasped; however, the weldability of this steel and various properties after welding The performance of this item is not clear, whether the welded joint can meet the product design and use requirements, and further work is needed to formulate a reasonable welding process.
In the 865mm blade, the rib boss structure is adopted. In order to ensure the frequency requirements of the blades, a group of 5 blades is used in the structure, and the welding connection of the rib bosses is used to reduce the natural frequency of the blades and ensure safe operation.