X5CrNiCuNb16-4 ESR Wrought billets or round bars, for subsequent cold cutting and hot forging into turbine blades
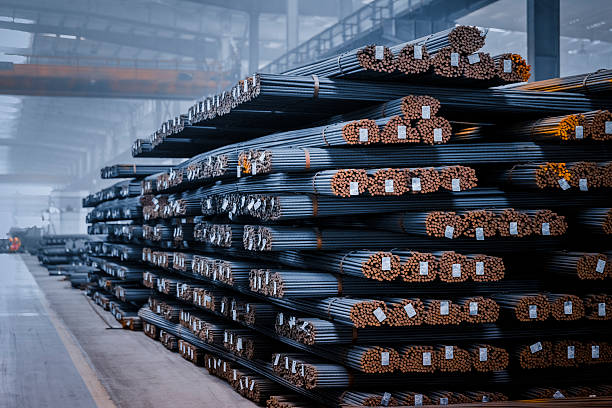
Keywords: X5CrNiCuNb16-4, X5CrNiCuNb17-4, AISI 630, 17-4 PH, S17400, 1.4542
Metallurgy: EAF, followed by AOD or VOD, followed by ESR
Process route and surface finish: Hot forged or rolled, overaged, descaled or rough machined (1E or 1X according to UNI EN 10088-3)
Applicable standards: UNI EN 10088-3, UNI EN ISO 6506, ASTM E112, SAE AMS 2315, ASTM E45, ASTM E381, UNI EN ISO 6892, UNI EN ISO 148, ASTM A 370, SEP 1923.
Material Properties Requirements:
Chemical Composition:
C | Si | Mn | P | S | Cr | Cu | Ni | Nb | Nb+Ta | N* |
---|---|---|---|---|---|---|---|---|---|---|
≤0.050 | 0.10-0.35 | 0.30-0.60 | ≤0.025 | ≤0.005 | 15.00-15.50 | 3.00-3.70 | 4.20-5.00 | 0.20-0.35 | 0.20-0.35 | 0.02-0.05 |
All the values are given in weight percentage [%]. Wherever not specified, no alloying addition should be made. * = Value of N to be reported in a separate sheet.
Microstructure
- The microstructure shall be uniform and fine grained across the whole product section.
- Chemical segregations resulting in linear indications, segregated bands, big size carbides (Ø ≥ 10 μm), carbides allignments, carbides precipitations at former austenitic grain boundaries shall not be accepted.
- Avg. grain size according to ASTM E112: ≥ 5.
- Fields with avg. grain size according to ASTM E112 < 3 shall not be accepted.
- Delta ferrite content according to SAE AMS 2315 < 0.9% on the worst field.
- Inclusions content according to ASTM E45, Method A:
A B C D Thin Heavy Thin Heavy Thin Heavy Thin Heavy 1 0.5 1 0.5 1 0.5 1 0.5
Expected mechanical properties
Rp 0.2 %
[MPa]Rm %
[MPa]A5
[%]Z
[%]Impact Energy
[J]Hardness
[HB]FATT50
[°C] (**)930-1000 max 1040 min 13% min 50% min 100(*) 295-335 max -25°C
(*) = Avg of 3 specimens
(**) = meaning at least 50% shear below the indicated temperature. Shear percentage to be evaluated according to ASTM A 370. The FATT50 diagram shall be included in the certificate, the choice of points shall allow a consistent fitting, for example temperatures should lay over a span of 60 degrees, centered on the target value.