Dynamic Recrystallization of AISI 422 Stainless Steel During Hot Deformation Processes
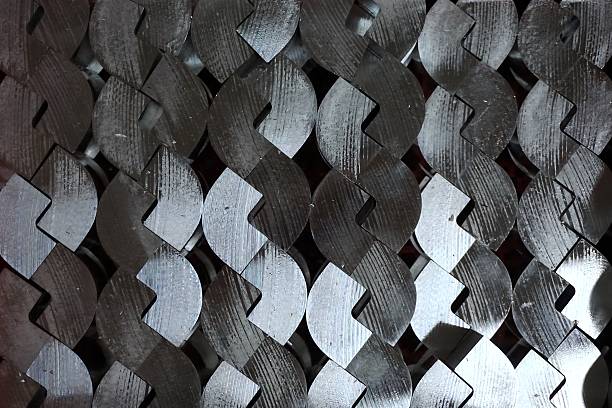
n this work, hot compression tests were performed to investigate the dynamic recrystallization (DRX) process ofa martensitic stainless steel (AISI 422) at temperatures of 950, 1000, 1050, 1100 and 1150oC and strain rates of 0.01, 0.1 and 1 s-1. The dependency of strain-hardening rate on f l ow stress was used to estimate the critical stress for the onset of DRX. Accordingly, the critical stress to peak stress ratio was calculated as 0.84. Moreover, the effect oftrue strain was examined by f i tting stress values to an Arrhenius type constitutive equation, and then considering material constants as a function ofstrain by using a third-order polynomial equation. Finally, two constitutive models were used to investigate the competency of the strain-dependent constitutive equations to predict the f l ow stress curves of the studied steel. It was con-cluded that one model offers better precision on the f l ow stress values after the peak stress, while the other model gives more accurate results before the peak stress.
The AISI 422 martensitic stainless steel is commonly used in relatively high operating temperatures (as high as 650oC) and under corrosive conditions. This fact makes this steel very appropriate for making high-temperature bolting, rotors and gas turbine blades (Ref 1, 2). The durability of the microstructures and mechanical properties of these parts is signif i cantly impor- tant as they are exposed for a relatively long time at high- temperature services (Ref 3). This steel was developed by modifying the chemical composition of the EI802 steel with the aim ofimproving its microstructural stability. It can be done by correcting its composition, namely decreasing the content of chromium from 11.0-13.0 to 10.5-12.5 wt.% and increasing the concentration of carbon from 0.12-0.18 to 0.17-0.23 wt.% and the concentration of nickel from 0.4-0.8 to 0.5-0.9 wt.% . In addition, optimum microstructure in terms of strength and ductility is crucial for production of steel parts, which can be provided by thermomechanical processing. In order to get this aim, the deformation process parameters such as temperature, strain per pass, strain rate and initial grain size must be well selected (Ref4-6). Two main softening mechanisms taking place during the hot deformation of austenite are dynamic recovery (DRV) and dynamic recrystallization (DRX), depending on the hot deformation conditions for a given microstructure (Ref 7). The latter mechanisms have a great inf l uence on controlling the microstructure as well as the f l ow stress of a material. In materials with low staking fault energy like austenite in stainless steel, the DRV kinetics is relatively slow, promoting dislocation accumulation and providing enough driving force for the onset ofthe DRX process after a relatively amount ofstrain is impaired (Ref 8, 9). DRX phenomena are acknowledged as an important feature to restore the ductility of the materials which are being work hardened during deformation process. DRX allows large deformation in the material without crack or damage appearance (Ref 10-13). Typically, DRX is favoured at high temperatures and low strain rates and is also acknowledged as a grain ref i nement mechanism under most forming conditions (Ref 14- 16). A new grain structure appears after DRX by formation and migration ofhigh-angle grain boundaries, and therefore promot- ing the grain ref i nement of the deformed alloy (Ref 17). Although the AISI 422 stainless steel has widely used in industrial applications, the hot deformation process ofthe steel has been less investigated and only little information on the f l ow stress behavior of the steel has been reported. Hence, the main goal of the present work is to investigate the effect of deformation parameters such as deformation temperature (in temperature range of 950-1150 ?C) and strain rate (0.01, 0.1 and 1 s?1) on the hot deformation characteristic ofthe steel. For this purpose, f i rst the effect of hot deformation conditions on the microstructures of the alloy was investigated; second, the critical stress for initiation of DRX was determined according to the method proposed by Najaf i zadeh and Jonas (Ref 18); third, a constitutive relationship was developed describing the dependence of the f l ow stress on the deformation temperature; and f i nally, two constitutive models were used for modeling of f l ow stress behavior of the studied steel
Table 1 Chemical composition of AISI 422 martensitic stainless steel
Fig. 1(a) Optical and (b) SEM micrographs of as-received microstructure of AISI 422 stainless steel