GTD-450 stainless steel during laser powder bed fusion
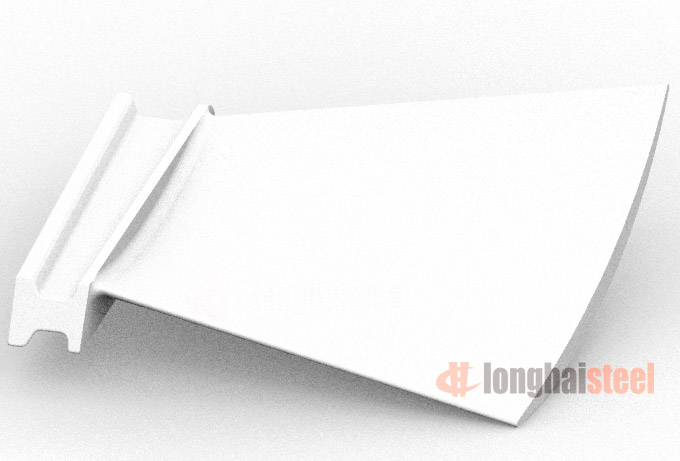
GTD 450 is a new type of maraging stainless steel. It has a wide application prospect in the additive manufacturing of complex components such as GTD 450 compressor blades using L-PBF technology. In this study, a multi-scale numerical model was used to simulate the whole process of L-PBF forming of GTD-450 stainless steel block. This numerical model can describe the evolution process of L-PBF forming temperature field, melt flow field and melt free surface. With the help of simulation results, the surface morphology of GTD-450 stainless steel formed under different layers is clarified. The experimental and numerical data of surface morphology are in good agreement, which verifies the reliability of the numerical model. Based on the experimental results, the influence mechanism of melt pool behaviour and thermal history on melt solidification behaviour was discussed, and the development process of L-PBF block surface morphology under the influence of melt pool behaviour was explained.
GTD-450 is a martensite precipitation hardening stainless steel, such as 17-4 PH and 15-5 PH, are strengthened by the precipitation of Cu-rich particles in the martensite matrix. GTD-450 not only has good corrosion resistance and high strength below 500 °C, but also has high toughness. It is mainly used as blade material for gas turbine of generator set. Due to the characteristics of GTD-450, only forging process can be used to improve the mechanical properties, but it is difficult to process high-hardness plates and bars into complex structural parts.
Laser powder bed fusion (L-PBF) has the advantage of realizing precision rapid forming of complex structures, and has become an important approach for fabrication of complex structures. In the L-PBF forming process, the grains of the formed parts melt and solidify rapidly, and the cooling rate in this process can reach 105 K per second. This characteristic of high cooling rate leads to the fine intracrystalline substructure of the formed parts, which makes the L-PBF formed parts usually have excellent mechanical properties. The L-PBF forming process is a complex interaction process between laser, powder and solid metal, the behavioral characteristics of the melt pool in this process are controlled by multiple physical fields such as temperature field, flow field and solute field, which leads to complex surface morphology, microstructure and solidification defects of the formed parts. Most researches on the surface morphology of L-PBF formed parts focus on the variation of surface roughness of samples with typical characteristic shapes with process parameters, so as to improve physical defects such as balling, spattering and cracking in the L-PBF forming process. At the same time, there are few systematic reports on how the process parameters affect the surface morphology of formed parts. In this study, the effects of process parameters on the evolution of L-PBF surface morphology were systematically investigated from both experimental and simulation aspects.
Chouhan et al. constructed a single melt track by varying the laser spot radius and scanning speed. An integrated 3D discrete element-computational fluid dynamics (DEM-CFD) model was used to simulate the melt track. According to the computational and experimental results, the authors optimised the optimal scanning speed and laser spot radius and obtained the minimum surface roughness of the single melt track. Feng et al. [1 established a coupled DEM-CFD model to study the evolution mechanism of surface roughness in the overhang region. They found that the evolution of the surface morphology is a comprehensive result of the border track contour, powder adhesion, warp deformation and dross formation, and is closely related to the overhang angle. Khairallah et al. [16] developed a three-dimensional high-fidelity mesoscale model of L-PBF forming and found that the physical phenomena involved in the forming process are closely coupled and all closely related to the temperature field. In subsequent research, it was found that pore defects are easily formed at the turning points of laser reciprocating scanning. The reliable simulation results provided by ALE3D software explained in detail the mechanism of pore formation at the turning point and developed a general mitigation strategy to eliminate this pore formation process and improve the geometric quality of the melt track. Ransenigo et al. used commercial CFD software FLOW-3D AM to perform single and multi-track simulations on Ti6Al4V alloy. The main data obtained are the shape and size of the melt pool, the morphology of the scan track surface and the porosity. In particular, a specific model is used to predict the ingress of air into the melt pool, thereby estimating the gas porosity and realizing the prediction of the porosity level of L-PBF formed samples through simulation.
Numerical simulation software such as FLOW-3D or ALE-3D can provide accurate simulation data for predicting L-PBF formed samples. However, due to the high computational cost, these models mostly focus on single-track prediction and rarely predict multiple layers. And the size of the computational domain used by these models does not match the actual size of the L-PBF formed part. Therefore, high-fidelity multi-physics simulations are currently limited to the mesoscale and have not been extrapolated to the macroscale. The HF-LBM multi-scale multi-physics numerical model used in this study can predict single-track solidification morphology in less than 1 h. Therefore, the computational domain can be extended to the macroscale and the overall multi-track, multi-layer process of L-PBFed blocks can be simulated while ensuring the accuracy of the simulation results. The multi-scale multi-physics model used in this study has been described in detail in previous work. This study focuses on the evoluti